What is a Kanban Board?
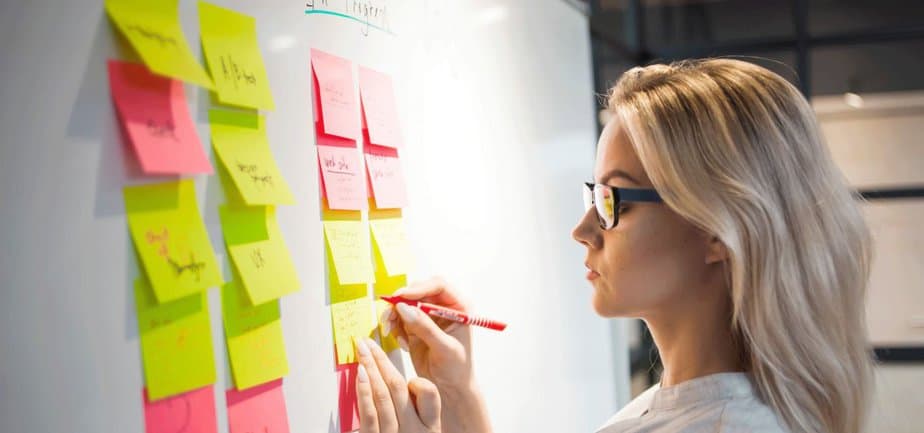
Having a Kanban board is essential to implementing Kanban in any business operation. A Kanban board that guides the team in consistently executing the core properties and principles of the Kanban method in their work.
What Exactly is a Kanban Board?
A Kanban board is a tool used to visualize the flow of work and enables a team to manage and optimize its processes. Kanban is the Japanese word for “visual card” or simply, “card”. The Kanban method originated in the manufacturing industry when Toyota re-engineered its car manufacturing process. To manage the flow of work-in-process (WIP) items within the assembly line, workers would use Kanban cards to signal the team from a preceding process when they are in need of parts. The preceding process team then knows WHEN to produce the parts and IN WHAT AMOUNT – limiting work in process goods and producing only what is necessary at the right time.
How Do Teams Use It?
Teams use Kanban boards to visualize and manage their workflow. The board maps key process steps and contains valuable information for members regarding their workload, priorities, deadlines, and expectations.
This visibility allows them to manage and improve the processes easier than traditional methods.
Elements of a Kanban board
A Kanban board mainly has two components:
- Workflow
- Kanban cards
Workflow refers to the process steps an item or task has to go through in order for it to be completed. The workflow is depicted on a Kanban board through columns and swim lanes. Kanban cards are then used to represent the task a team will work on. These cards flow through the columns and swim lanes of the Kanban board – allowing teams to know the status of their work at a glance.
A simple Kanban board has at least three columns – To Do, In Progress, Done
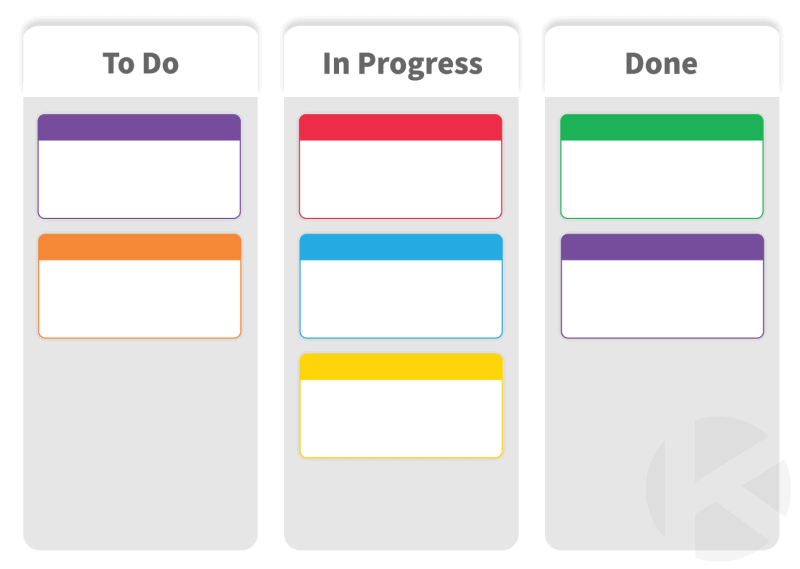
While this would work for simple processes, the majority of real-life business processes have various process steps to get the work done. A single In Progress lane would not be very effective in managing and optimizing your workflow as there is not much visibility on the processes that actually take place within this state.
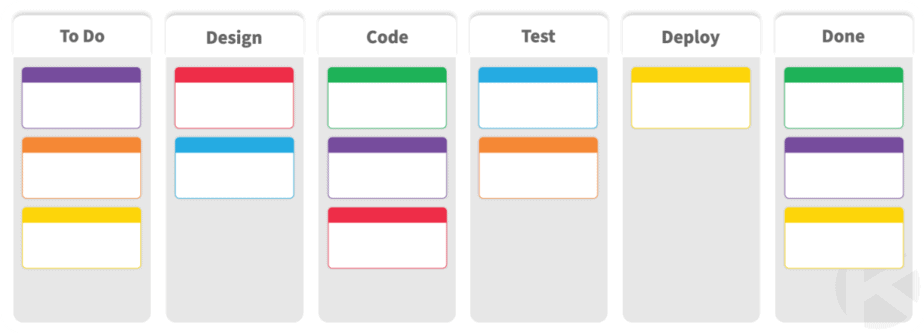
At the minimum, Kanban cards contain the task name and the names of the team members working on the card. It can also contain effort estimates like the number of work hours or t-shirt sizes. To easily distinguish a card and not have to refer to lengthy task names, a unique identifier is normally used.
Physical or Virtual board?
A physical board would work well for co-located teams as collaboration happens personally and instantaneously as the team is gathered in front of the board. On the other hand, distributed teams would definitely need and benefit more from virtual Kanban boards built with the help of Kanban software as they need to collaborate online to stay aligned with their goals despite distance barriers.
For those who opt to use physical boards, a whiteboard, some pens, and post-its would be sufficient to get your Kanban board going. You can also use color-coding to identify what type of task is being worked on. In software development, for example, teams can use different colored cards to show if they are working on a feature, a bug, or some other technical task. Visual signals such as colors can also be used to show the priority level of a task so that teams would easily know which to task to pick first.
For remote teams, virtual Kanban boards are equipped with various features that make it easy for teams to customize their boards based on their workflow. You can see an example of the Kanban board for software development we used when building Kanban Zone.
Online Kanban boards also usually have various functionalities to tag cards with all the necessary information to get a task done. This card from a Kanban Zone board, for example, allows teams to indicate due dates, specify the priority level and the estimated effort or size needed to do a task. Teams can also indicate when a task is blocked in any way. Collaboration is also seamless in the application with commenting and attachment features.
Putting your Kanban board to work
Visualizing work through a Kanban board allows teams to articulate what gets an item to pass a step and be eligible to be pulled on by the next step in the process. This enables a consistent and standardized application of the process and ensures no step is missed.
As the board is accessible to everyone on the team, it promotes transparency and teamwork. Even stakeholders can easily know how a project is progressing just by looking at the board. With Kanban boards holding valuable information about a team’s work, it is also an ideal tool to bring to meetings to make them more productive and focused.
As you go through your work using a Kanban board as a visual indicator, you will get to learn more about your process efficiency. The board will tell you the capacity that each process step can take on at a given time and where work is piling up. This will help you to set your WIP limits.
Setting WIP Limits
Work in progress (WIP) limit is the amount of items that can be started at a certain stage. WIP limits are very helpful because they require you to finish one thing before moving on to another.
That’s why you need to explicitly state in your Kanban board how many items can be worked on per step in the workflow. Limiting the items worked on at one time allows teams to focus on getting things done and prevents them from coming up with half-baked goods. As the team matures and gains more knowledge and skills necessary to build the product, WIP limits can change. It is therefore important to regularly review how your team is managing the workflow.
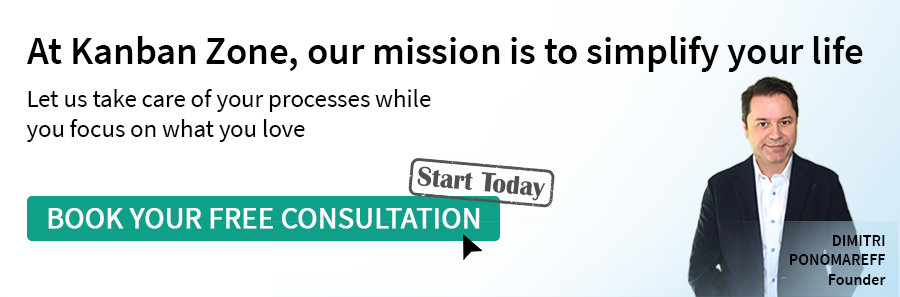
Measuring Team Performance with Kanban Metrics
There are a number of metrics that help teams assess how they are going about their work. Lead times, cycle times and throughput are good information radiators that are used in the Kanban method.
- Lead Time. The period it takes from a customer filing a request until he gets the final product.
- Cycle Time. The period it takes an item from when it entered the process until it gets out of the process completely.
- Throughput. The amount of work that comes out of the process.
To visualize lead time and cycle time, let’s take an example of a maintenance software team. The time an end user files an issue ticket starts the lead time clock but doesn’t necessarily start the cycle time clock because the team may not be able to do the task of resolving the issue right away. The issue ticket remains in the backlog or the list of To Do items until it gets picked up by the team. When the team pulls the issue ticket from the To Do bucket to the first step in the process, that is when the cycle time starts. Once the item goes through all the steps in the Kanban board and gets to the Done bucket, the cycle time ends. The lead time ends when the code fix is deployed to the Production environment; fulfilling the end user’s need.
Measuring your lead time, cycle time and throughput will help your teams estimate completion times of work coming into your value stream. This will also help your teams come up with more accurate WIP limits. Having these metrics at hand will also help teams spot areas for improvement.
Equally important as gathering these metrics are ensuring you have feedback mechanisms built into your team’s processes. Make it a point to discuss these metrics with your team and encourage collaborative action. The point here is to not put your metrics to waste and let them just be a number that doesn’t mean anything for your team. Use them to trigger the evolution of your process.
A continuous improvement mindset is definitely instilled through implementing the Kanban method. Let your Kanban board guide you through that process and enable your teams to evolve towards higher productivity and better results.