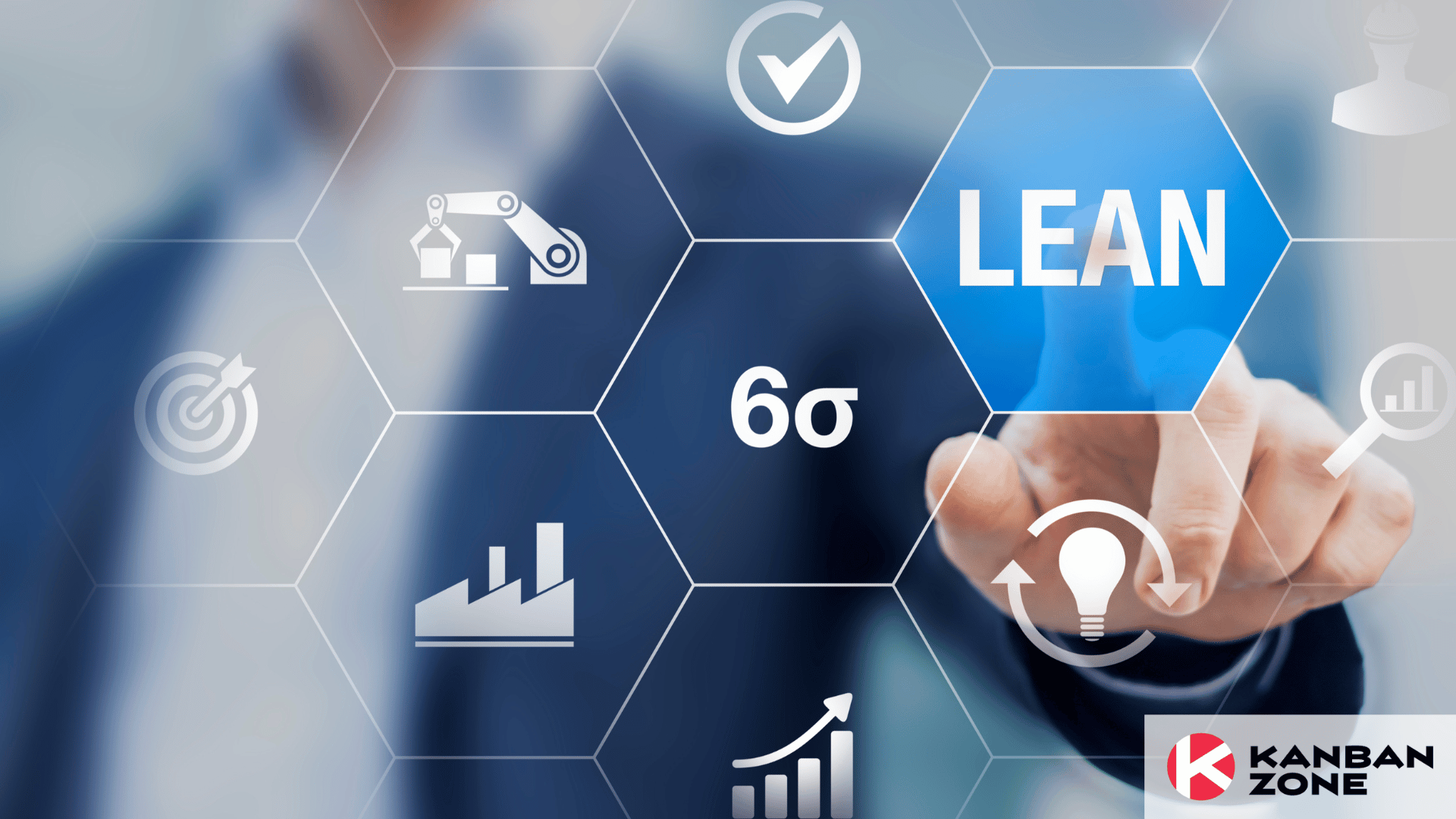
Have you ever wondered how to improve customer satisfaction rates and to manage your business effectively while avoiding wastes of different kinds that may hinder process efficiency? Then, Lean management could be the right path to follow.
In this article, we take a look at what Lean management is, its principles, advantages and possible tools.
What is Lean Management?
Lean management refers to a type of business approach that aims at improving efficiency and customer satisfaction by decreasing the time of non-value-added activities while optimizing process workflow. In other words, lean management is understood as a way of allowing a business to get more productive, better organized, and with improved processes. Due to its versatility and achievable results, Lean management has found applicability in many different business segments, for example, manufacturing, software development, engineering and healthcare.
Having its origins and principles based on the Toyota Production System (TPS), businesses have achieved significant improvements concerning cycle time, lead time, productivity, and profitability.
The main goal of Lean management is to help businesses to deliver products or services presenting high value through the customers’ perception and to reduce waste, namely known as, defects, rework, overproduction, improper processing, unnecessary movements, redundant transportation, unbalanced inventory, intellectual waste and waiting time.
Now that you already know what Lean management is, let’s take a look at its main principles.
5 Lean Management Principles
To effectively apply Lean management in your business, it’s fundamental to understand the main principles of Lean management, as shown below.
1. Defining Value
In Lean management, the definition of value is based on the customer’s point of view. This means you need to understand which are the basic requirements in order to develop and deliver a product or service. Put simply, in this context, value is totally related to what the customer is really willing to pay. Therefore, activities or even processes that are not needed neither by the business nor by the clients are considered as waste and must be eliminated.
2. Mapping Value Stream
Here is where you map the whole process for delivering a product or service including all process steps and activities that either add value or do not necessarily add value to the final product or service. It is important to document the mapped processes and activities in order to identify what can be improved or eliminated. By mapping the value stream, it is possible to better understand critical business processes and check possible bottlenecks and wastes that may exist which hinder the final process outcome.
3. Creating Continuous Workflow
This principle refers to developing and delivering work without interruptions, so that customer needs can be attended to in the shortest time as possible, without sacrificing the required quality of products or services to the clients. Creating a continuous workflow often requires time and team effort in order to accomplish it in the right way. If implemented correctly, continuous workflow can lead to optimized deliveries, customer satisfaction and consequently business profits.
4. Implementing a Pull System
In a pull system, work is developed only in case there is a real demand by the client, where the client can be either internal to the business process (e.g. departmental teams) or the final customer of the business. By implementing a pull system, business resources can be saved and wastes in the form of overproduction can be avoided.
5. Establishing Continuous Improvements
Also known as Kaizen, continuous improvement is a principle related to the never-ending search for improvements in the business process as a whole. By establishing continuous improvements throughout the business processes, greater customer satisfaction can be gained which increases customer loyalty and leads to positive business outcomes. Therefore, it is important to motivate team members to get involved in continuously improving processes on every single level of an organization.
Why Implement Lean Management Principles
By using Lean management within your business, several benefits can be obtained, such as:
1. Improved quality
As a result of detecting and getting rid of defects that may exist within business processes, Lean management affords significant improvements in quality for delivered products or services.
2. Increased agility
This results from applying the principle of implementing a pulled system as mentioned earlier. By implementing a pulled system, business lead times can be decreased.
3. Higher engagement and focus
Both higher engagement and focus of team members can be achieved when using Lean management, due to the encouragement of teams to check for possible problems occurring in business processes. After identifying problems, they must be collaboratively solved by the teams which in turn leads to more focused activities and higher team engagement.
4. Increased productivity
This benefit has a lot to do with two of the previous principles: mapping value stream and establishing continuous improvements. By understanding critical business processes and improving them continuously over time, increased productivity can be achieved by eliminating, for example, existing waste and by streamlining business processes.
Make Kanban a Part of Your Lean Management Tools
Nowadays, many different Lean management tools are available to help businesses, for example, value stream mapping (VSM), 5 Whys root cause analysis, 5S method and many others. Besides these tools, the Kanban method is a possible alternative to support Lean management in businesses in different segments. This is mainly due to the fact that the Kanban method supports all the principles of Lean management mentioned earlier thus helping businesses in their journey of continuous process improvement.
Learn to Work Smarter, Not Harder!
Get our top articles weekly.
Table Of Contents
Discover many more posts…