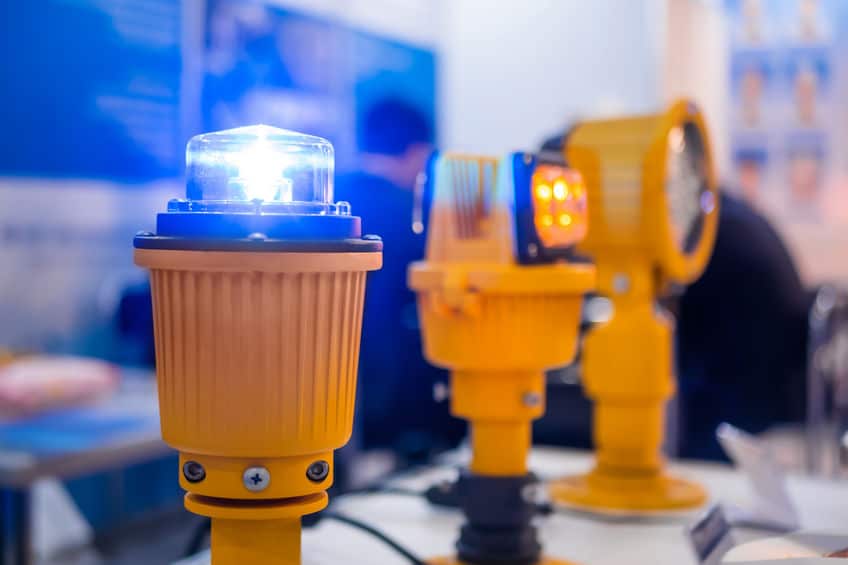
We can thank the pioneers of the Japanese manufacturing industry for their relentless pursuit of efficiency and quality. Their innate drive towards high levels of quality and zero waste has paved the way for the birth of the Toyota Production System and Lean Manufacturing. And up to this day, we see these concepts and practices applied in businesses worldwide. One of the thirteen pillars of the Toyota Production System is called andon. Let’s explore how an andon system can help you improve quality in your workflow and why you should set up one.
What is andon?
An andon system is a tool that is used to signal when something is wrong in a production process. In Japanese, the term andon is translated to “light” or “lamp.” The idea for an andon system in a production line is that it lights up to alert workers that an anomaly has occurred in the process.
An andon system is central to applying the jidoka principle, another pillar in the Toyota Production System. Jidoka means “automation with human touch” or what we call autonomation. It’s the ability of machines to stop a process when an abnormality is detected so that human intervention can come in and resolve the issue.
Using an andon to signal abnormalities coupled with the ability to stop the product line are the initial steps to performing jidoka.
5 Benefits of Using Andon at Work
If you’re looking to improve the level of quality and efficiency of your work processes, here are 5 benefits of using an andon system at work.
Stop defects as soon as they happen
With an andon system in place, you can immediately be flagged when an abnormality such as a product defect is detected. With this, you can lessen the defects that are being churned out by the production line. You will also prevent the risk of these product defects from ever getting into the hands of your customers.
Prevent recurrence of issues
An andon system helps you get to the root cause of problems. As soon as the production is halted, you can investigate the occurrence and identify the next steps to prevent the recurrence of the issue.
Reduce downtime
As you get to the root causes of problems and eliminate them, you will also reduce delays and downtimes in your processes. This will also reduce the costs associated with those delays and downtimes.
Empower your team to continuously improve
An andon system is not a tool for your machines. It is a tool that aims to empower your teams to be accountable for their processes and systems. It is a tool that enables them to stay on top of the process and look for ways to continuously improve it.
Improve overall productivity and efficiency
As you fine-tune your process, your overall productivity will increase. Your teams are more empowered to take on process issues instead of waiting for a supervisor or manager to intervene. Your machines will have better performance and uptime. Most importantly, the quality of your products will improve. This in turn will increase the value you provide your customers as well.
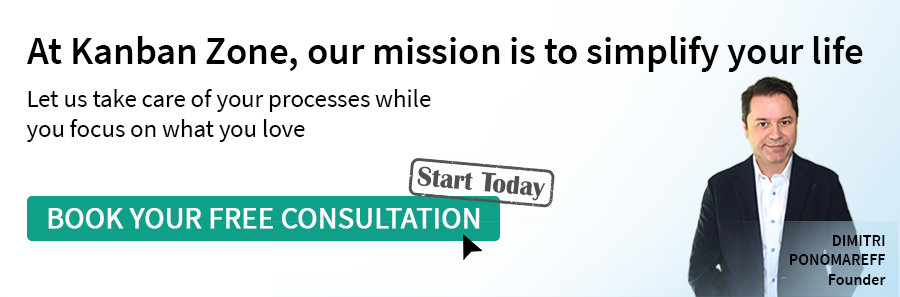
Setting up an Andon System
Now that you know how an andon system can help you and your teams, you might be wondering how you can set one up.
An andon system can be a digital dashboard connected to your production line that displays its progress and alerts the production floor of any anomalies. It can also be a built-in indicator or light that turns on when something is wrong with a machine. Sometimes an accompanying sound is used so the event is both seen and heard on the entire floor. An andon system can be any visual indicator that would signal machine problems or production abnormalities.
But to be fully effective, setting up an andon system needs to be done as part of a jidoka process. We have four steps when applying jidoka:
- Discover an abnormality
- Stop the process
- Fix the immediate problem
- Remove the root cause.
Your andon system will be used in steps 1 and 2. Depending on whether you’re using an automatic or manual activation. Automatic activation means your andon can immediately stop your process as soon as an abnormality is detected. Manual activation means a worker needs to manually stop the process, usually through a button or cord.
But it’s important to note that having an andon system is not enough. There must be a plan on how the problem will be fixed so that production can resume and later on won’t be stalled by the same reasons. This is where steps 3 and 4 come in.
While we can’t guarantee that no defects or abnormalities will come out of our process, we can take a more proactive approach to how we handle and resolve them. Apart from using an andon system, you can also use poka-yoke to prevent errors before they occur.
Andon, poka-yoke, and jidoka are tools and concepts that teams can use to improve the way they work. But they are not silver bullets. They will signal what’s wrong but it’s up to the teams to take action. Let these tools help you and empower your teams to take control of your work and improve your quality and efficiency.
Learn to Work Smarter, Not Harder!
Get our top articles weekly.
Table Of Contents
Discover many more posts…