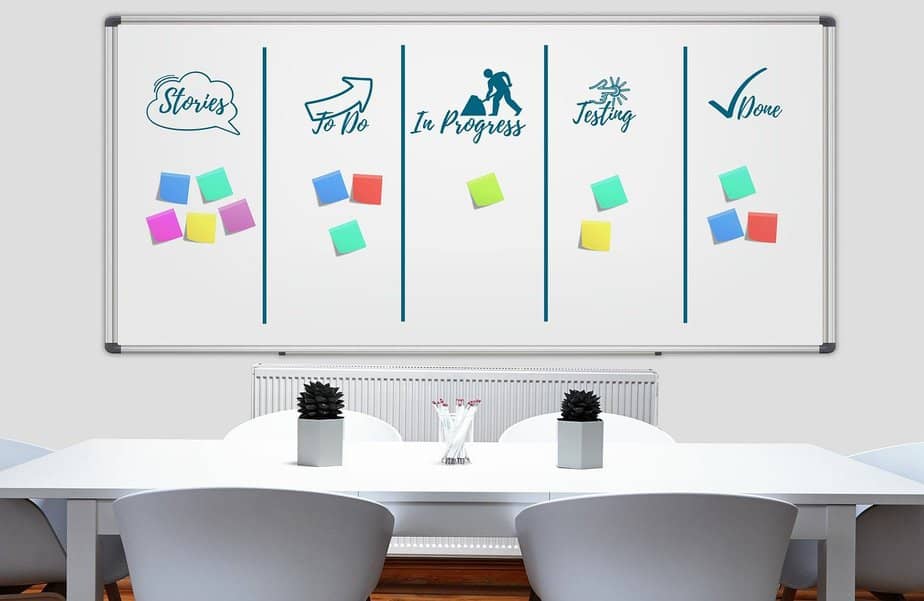
Managing business processes using Kanban can only be effective if it’s implemented properly. An effective Kanban system is more than just sticking post-its on a board. It is a mindset – a move towards productivity, organization, and eliminating waste through a steady flow of work. This is where the six rules of Kanban can come in handy.
A strong level of trust between leadership and staff is important to establish a steady flow of work. But in order to achieve a high level of trust within the organization, expectations must be set. We need a guide so everyone in the team knows how to do their work properly. The six rules of Kanban will guide teams towards a successful and effective Kanban system implementation.
If you are serious in your Kanban practice, you need to ensure that these six rules are consistently followed in every business process you operate
The Six Rules of Kanban
Let’s explore the six rules of Kanban and how they both apply to traditional production and knowledge work.
1. Never Pass Defective Products
Upstream processes shouldn’t pass products that do not meet the standards and level of quality expected. Defective products should be removed from the production line and be dealt with outside of it. This ensures that only quality products go to your customers, lessens waste, and decreases customer complaints.
Policies help ensure that the desired level of quality is maintained at every step. This is fairly straightforward for tangible goods production. But the same applies to knowledge work.
For example, in software development, applications go through rigorous quality assurance testing before they’re released. There can be functional, regression, integration, performance, and stress testing to name a few. If the team agrees that all features and enhancements need to pass these levels of testing, then that’s the only time they can release them to market.
2. Take Only What’s Needed
A successful Kanban implementation requires that downstream processes only pull what they need. This prevents overproduction, lowers costs, and makes operations more reflective of the demands of the market.
Applying this rule as one of the six rules of Kanban is fairly straightforward for manufacturing processes. For knowledge work, we can see this as only working on customer requests or orders when needed. This also means following the priority in your backlog.
3. Produce the Exact Quantity Required
Rule #3 of the six rules of Kanban works hand-in-hand with rule #2. Taking only what you need would lead to only producing the exact quantity of products that are required. If you overproduce, what are you going to do with that excess inventory? You’re stocking up on more costs. These include opportunity costs from the resources and money spent to build the item, storage costs, and transportation costs. You also run the risk of having the product deteriorate or become obsolete.
How does this apply to knowledge work? Having a Minimum Viable Product (MVP) mindset helps in this area. If a customer wants to have the facility to download a report from your app, you don’t need to throw in a print feature as well. Focus on the minimum requirements. You can build on the product as the market demands or as your product direction leads you to it.
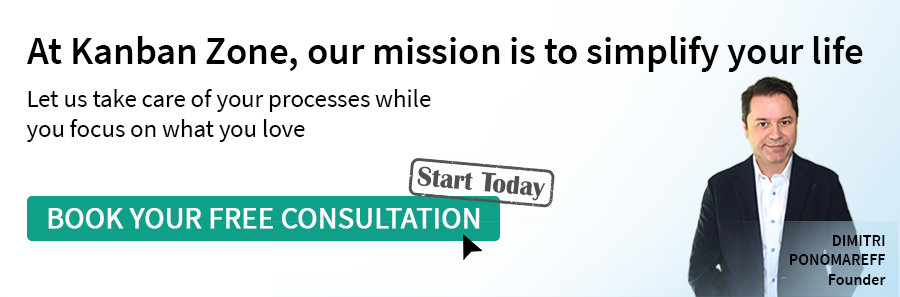
4. Level the Production
In order to achieve a steady flow of work, all units within the Kanban system should only produce the number of items based on the capacity of its limiting contributor. Illustrating this in the manufacturing setting, machine A can produce 500 units but machine B, its subsequent process, can only process 300 units at a time. If we let machine A produce 500, a bottleneck will be experienced in machine B. To solve this and let work flow smoothly, we must limit machine A’s production to 300. You can explore Heijunka, another Lean concept, to see how you can level your production activities.
In knowledge work, we can see leveling by measuring the capacity of every step in your Kanban. When you spot a bottleneck, you can alleviate the burden by augmenting your resources or setting your work-in-progress limit based on your limiting contributor.
5. Fine-tune the Production or Process Optimization
Once the team has initialized its Kanban implementation, the next aim should be to utilize their Kanban system to surface pain points and improvement opportunities. This would require a closer look at how work is flowing and measuring their performance.
Kanban metrics such as lead time, cycle time, and throughput will help teams get a quantitative and objective assessment of their work. A cumulative flow diagram will help teams spot bottlenecks. Online Kanban tools, such as Kanban Zone, have these metrics and reports built-in. Teams must use the tools available for them to make informed decisions on how to optimize their process. They must look for activities that produce waste. This can be in the form of delays, defects, rework, and unnecessary handoffs to name a few. Regular team retrospectives where teams discuss their experiences, pain points, and improvement suggestions and then formulate solutions to address them are key to fine-tuning production.
As inefficiencies decrease, work-in-progress items also decrease because the process is leaner.
6. Stabilize and Rationalize the Process
When you ensure quality, level production, and optimize your process, your process gains stability. A stable process enables standardization. You should document your process so that there is a common shared understanding of how your team should operate. Any deviations to the process standards should be managed by policies.
Having your standards explicit provides a strong foundation for your team to operate with predictability and consistency. Your policies and standards can evolve through time as you continue to fine-tune your process. Have regular team reviews to update your process and make your Kanban system more robust.
Ready for a Successful Kanban Implementation?
When teams adhere to these six rules, they are more empowered to harness the benefits of Kanban. The power of Kanban lies in the quality of its implementation. When you take the six rules of Kanban to heart, you reduce waste, optimize your resources, become more cost-efficient, and maximize your productivity.
Learn to Work Smarter, Not Harder!
Get our top articles weekly.
Table Of Contents
Discover many more posts…