Kanban Pull System
A Pull System is a lean technique used to control the flow of work by only replacing what has been consumed. This means that the trigger for work to be done is when a customer demands for it.
To better visualize a Pull System, take for example, a vending machine. Products will only be replenished when the stocks have run out. The suppliers won’t overstock the vending machine because each lane has a set capacity. If there is no product demand, they won’t replenish it.
In the vending machine example, the customer pulls products from the vending machine. Having an empty rack is a signal for the vending company to tap their brand partners to replenish their stocks. Therefore, the vending company also pulls products from the brand partners. All these happen because they act according to customer demand.
This is precisely how a Pull System should work.
Push vs Pull
Traditional companies often use a Push System, choosing to have products ready “just in case” there is a demand for it.
In most manufacturing companies, products are created based on forecasts. Batches of products are created in the hopes that they will be entirely consumed by buyers. The problem with this strategy is that forecasts do not necessarily reflect actual demand. Quite often, they will be higher than actual demand.
Forecasts that are greater than actual demand can lead to excess inventory and additional costs to store and manage it. This can cause businesses to sell the surplus at a reduced price, sometimes even lower than the manufacturing cost, just to recoup a percentage of their efforts.
When demand is higher than the forecast, businesses would then be left to speed up or overload the production line to meet the requirements. This leads to overburdening and unevenness in terms of the workload, or what they call Mura and Muri in Japanese.
While implementing a Push strategy may be based on good intentions, it is not always cost-effective. It requires people to work based on anticipated demand, which can lead to overproducing. The business allocates resources to create products, but the return on investment is not guaranteed, leading to unnecessary costs and waste.
Pull Systems are the complete contrast of Push Systems.
When production uses a Pull strategy, work is based on actual customer demand. Teams focus on producing smaller lots instead of allocating resources to make larger batches. This makes them nimble and better able to work through changes in demand. When the Pull System is implemented, inventory is minimized, if not eliminated. The Pull System also helps teams become more focused rather than doing multiple work simultaneously. This allows teams to be more productive because they operate based on their actual capacity.
Pull Systems allow businesses to operate and deliver work “just in time”.
Just In Time is another lean manufacturing concept that prescribes production to be executed only when the customer wants it, in the amount that the customer demands, and without it being delayed in inventory. Pull Systems enable teams to deliver work “just in time.”
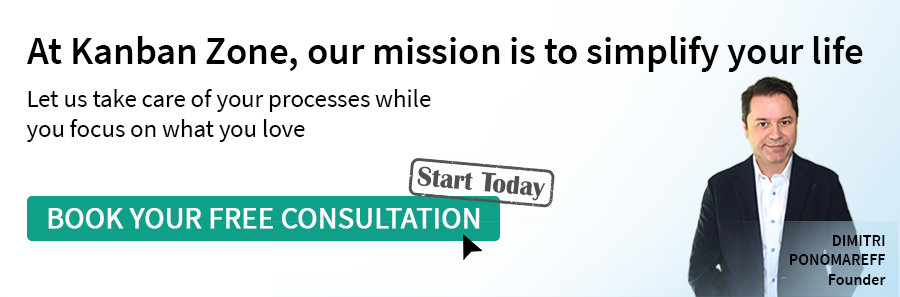
Kanban Pull System
Kanban is the most widely used Pull System framework. This is primarily because of its application simplicity and overall effectiveness in delivering results. It is also one of the most popular, with its introduction dating back to the inception of the Toyota Production System. Although it was originally applied in the manufacturing industry, Kanban is now used by organizations and teams from various industries.
Kanban has 5 core properties that guide teams in implementing this technique and ensure a proper Pull System is in place:
- Visualize the Workflow
- Limit the Work-in-Progress (WIP)
- Measure & Manage the Flow
- Make Process Policies Explicit
- Use Models to Recognize Improvement Opportunities
Implementing a Kanban Pull System
It is crucial that the 5 Kanban properties are embedded in your process to implement a Pull System successfully. Let’s explore what each of these properties entails to help you establish a working Kanban Pull System.
Visualize the Workflow
Before establishing any Pull System, and specifically Kanban for that matter, it is essential that you know your process. Mapping your process through a flowchart will help you visualize the exact steps that get your raw materials or ideas to become actual products.
The process flow is also vital in designing your Kanban board, the main tool for implementing Kanban. The basic Kanban board only has three columns – To Do, In Progress, and Done. While this can be used to start, it does little to help you identify improvement opportunities in your workflow.
Establishing a steady stream of work through Kanban can only be achieved when you can remove inefficiencies, bottlenecks, and unnecessary waste in your process. Having a high-level Kanban board with three columns will not help you surface those improvement opportunities.
Your goal should be to flesh out what that In Progress state entails. Gather your team and map your process flow together. The process actors will be best placed to determine which steps go into the Kanban board.
Once your Kanban board is ready, start creating task cards and establish pull guidelines in your system. Have your team pull in work when there is a demand for it. This will enable your team to satisfy customer needs at the right time.
Limit Work-in-Progress (WIP)
Introducing WIP limits to your workflow will help your team focus on the current task and prevent them from task switching. WIP limits should be reflective of your team’s capacity. While it may be challenging to get it right the first time, that is not the point. Regularly reviewing how workflows go through your system allows you to adjust your WIP limit to what is appropriate for your team.
Improving your Kanban Pull System
The other three properties are designed to help you better manage your Kanban Pull System and seek continuous improvement.
As you go along your Kanban practice, you will start to gather data about how you do your work. These metrics will help you assess how efficiently your team is completing the work and will influence process changes and improvements. Of course, to leverage Kanban metrics, you’ll have to abandon your physical board and leverage a Kanban software solution that collects workflow data. It is also recommended that you introduce Pull Signals within your Kanban System to manage the flow of work better.
What do these Pull Signals mean?
A Pull Signal is a clear indicator that a task item is ready to be pulled by the next process step. Some teams use Pull Signals, such as an internal Done column.
For example, we have a software development process. Within the Coding step, there is an In Progress and a Done column. The Done column signals the person in charge of the Testing step that any work item within this column is ready for testing.
Done columns signal the next person in-charge of the process step to pull from the preceding step
Using Pull Signals will help prevent your team from pushing work through the process and enable them to apply the Pull System mechanics since they will pull the work as needed.
Process policies enable your team to be consistent in its Kanban practice. It helps overall workflow management and sets the guidelines for how the team should work. Process improvement models, such as Kaizen, Six Sigma, and Value Stream Mapping, will help refine your Kanban Pull System. Coupled with the Kanban metrics you will gather, these models will help you surface and address bottlenecks and inefficiencies in your process.
These properties must be in place for a successful Kanban Pull System implementation.
Benefits of a Kanban Pull System
Using a Kanban Pull System has its share of benefits. Let’s explore each one of them.
- Eliminating wastes in the form of excess inventory, storage costs, and excessive handling, to name a few
- Shorter lead times
- Ability to be flexible and respond faster to changes in customer requirements
- Ability to scale the capacity of the team
- Establish predictability in terms of work completion
- Increase productivity due to focused work
Implementing a Kanban Pull System can be a strategic and effective approach to optimize your team’s resources. Meet customer demand at the right time, with the right effort, and in the right quantity with a Kanban Pull System.