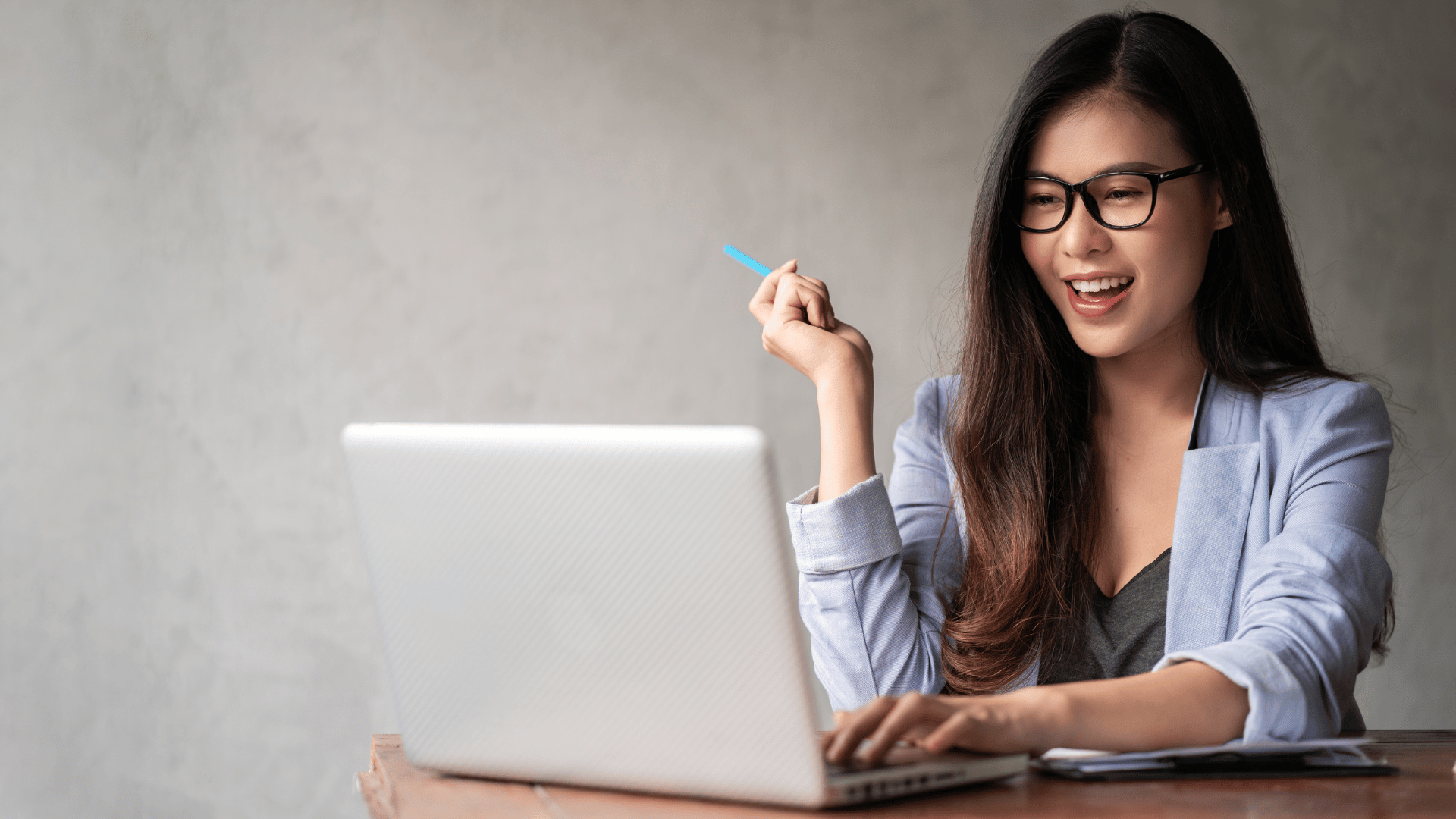
In order to stay competitive in their segments of work, nowadays businesses and companies usually face extreme push towards constant innovations and high flexibility to adapt to the never-ending changes due to economic, social and technological challenges.
With the aim of accomplishing these demanding requirements, it is crucial that organizations support a culture of continuous process improvement so that their processes can get more efficient over time. This can often be achieved by using appropriate methodologies, methods and training staff for the continuous process improvement mindset. One of such commonly used methods is the so-called Kanban method.
At this point, some intriguing questions may arise: What is continuous process improvement all about? How do you take control of your continuous process improvement by using the Kanban method? These topics are discussed in more detail in the following sections of this article.
The need for continuous process improvement
Put simply, continuous process improvement can be understood as a constant work to enhance the performance of existing processes that deliver either products or services in different business environments, as for example, in the manufacturing industry, software development, health and many others.
Over time, the effort to improve the process under consideration can either aim at incremental gains or even at totally innovative advancements regarding process productivity, quality as well as employee and customer satisfaction.
Due to the inherent dynamic environment that business processes often are subjected to, they will rarely present a constant and flawless performance. This means that variation is part of the nature of processes, therefore there will always be room and need for process improvements.
Kanban method as a tool for continuous process improvements
Initially conceived as a Lean Manufacturing tool, the term Kanban has a Japanese origin meaning “signs” or “sign board” and consisted in a method for scheduling production based on a signaling board which enables the manufacture or removal of production items in a pulled system.
In a more general view, the main functions of the Kanban method within a process are related to the visual control for the execution of tasks in an accurate and efficient way.
Continuous process improvements can be achieved by applying the main principles and common practices dictated by the Kanban method. Among the main principles related to the Kanban method are:
- Start with what you do now. This means that firstly, you can begin using the method exactly with the process your team is used to employing in daily activities.
- Agree to carry out improvements through incremental change. Here the team commits to continuously improve the process and plan the “to-be” state of the process in the future.
- Respect the current process, roles and responsibilities.
- Promote leadership actions at all levels. Any team member can act as a leader based on their expertise.
In the Kanban method, common practices help teams in their journey of continuous process improvements. Some common practices of the Kanban method are as follows:
1. Visualize Workflow
Visualization of the workflow plays an important role to identify improvement opportunities and effective collaboration in the project team. Besides, it also allows transparency which in turn leads to better team cooperation and a sense of being part of the process.
2. Limit Work in Progress (WIP)
By limiting the WIP it is possible to balance the utilization of resources and guarantee a better workflow of tasks in the process. This also affords to achieve a “pull system” rather than a “pushed system”.
3. Measure and Manage Workflow
The main idea behind measuring and managing the process workflow is to get a suitable rate of work and at the same time to finish the required amount of work efficiently. Additionally, work predictability can also be inferred easily through correct workflow measurements and management.
4. Make Process Policies Explicit
Explicit process policies aim at helping the team to understand how the work is organized. This allows the comprehension of how much, when, by whom the work should be done. The definition of explicit policies needs to be agreed in accordance with all the parties involved in the process.
5. Improve Experimentally
The Kanban method allows process improvements through continuous transformation. This can be done by means of designed experiments based on the various metrics that the Kanban method uses as a way to infer the actual state of the process.
Take Control of Your Continuous Process Improvement with Kanban method
The Kanban method allows you to take control of continuous process improvements. Among the many alternatives that the method offers, digital Kanban boards are very often used to accomplish this purpose.
By using digital Kanban boards, it is possible, for example, to visualize the entire process workflow in a faster way which in turn helps the project team to detect potential issues and bottlenecks in the whole process. This can serve as a way to further improve the process by taking collaborative actions jointly in the team.
Another way to continuously improve your process through digital Kanban boards is by analyzing specific Kanban metrics which are easily and promptly available when using these boards. After analyzing important Kanban metrics like lead time, cycle time, throughput and work in progress (WIP), effective actions can be planned by the project team in order to continuously improve the process performance.
Learn to Work Smarter, Not Harder!
Get our top articles weekly.
Table Of Contents
Discover many more posts…