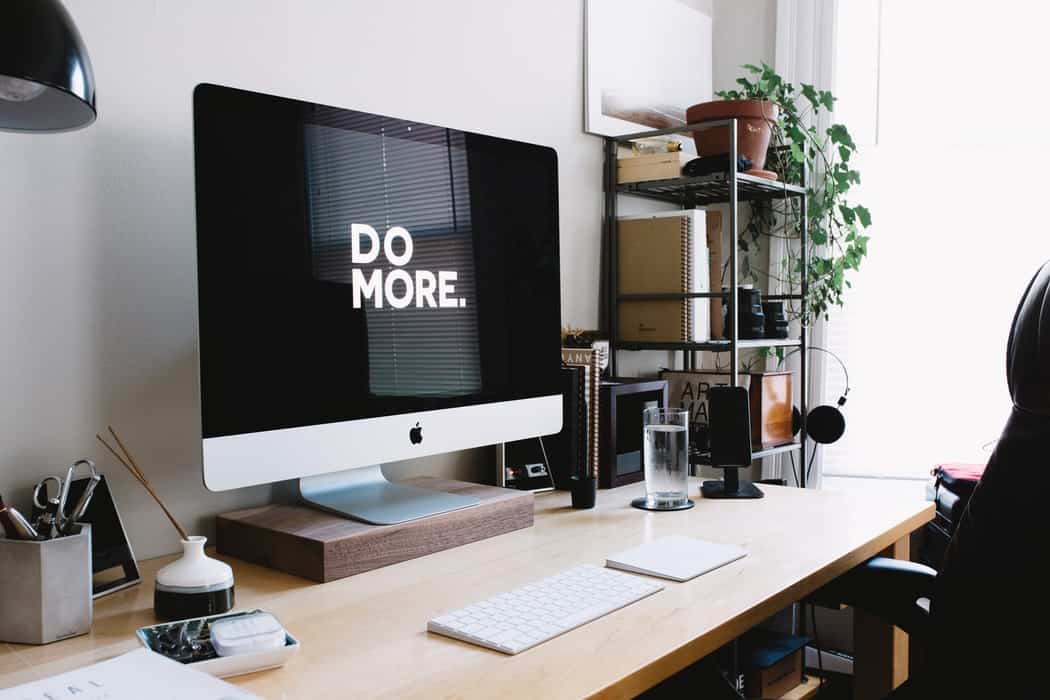
If you’re dealing with business processes and systems you will have most likely encountered Little’s law. The topic also commonly pops up when discussing process improvement and project management methodologies. You might even have a favorite Little’s law example that you use during your discussions. When you look at Little’s law, it doesn’t seem like a powerful concept. “What could an equation with three variables do?” is what most might think. But once you understand and embrace Little’s law and what it can do for your business processes, you’ll realize just how useful a three-variable equation can be.
What is Little’s Law Used For?
We discussed Little’s law in a more in-depth manner on this resource page. We also used a simple Little’s law example in that article to help you get up to speed with the theorem.
To recap, Little’s law states that the average number of items within a system is equal to the average arrival rate of items into and out of the system multiplied by the average amount of time an item spends in the system.
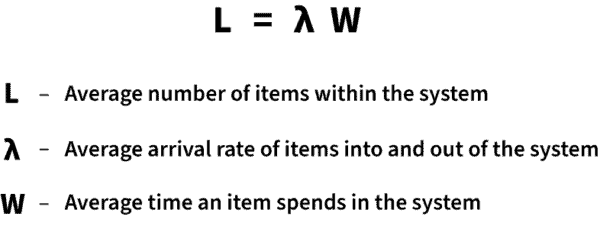
This theorem applies to any queuing system. Common Little’s law examples include production or assembly lines, airport queues, coffee shop queues, hospital lines, FIFO and LIFO systems, and Kanban systems. Basically, any process that looks like this:
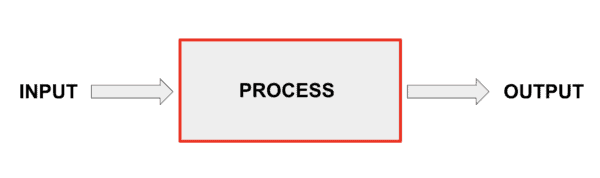
Little’s law can be seen in action for any process that takes in an input, performs some kind of service or process to transform it into a desired output.
Little’s law helps businesses understand their process capacity and performance. In our Little’s law resource page, we talked about the variables as it is expressed by the three Kanban metrics namely, Work-in-Progress, Throughput, and Lead Time. Knowing how your process measures up based on these three metrics will help you diagnose problems and plan your improvement initiatives.
Lead Time in a Kanban System and Why It’s Important
From our Input-Process-Output diagram in the previous section, we can visualize lead time as the time it takes from the input to enter the system, be processed, and exits the system as the desired output. The moment the item enters your Kanban system, whether you start working on it or not, the lead time counter starts to kick in.
If we take a pizza shop as a Little’s law example and focus on its order fulfillment process, lead time starts as soon as the customer places the order. Between a lead time of 45 minutes and 20 minutes, which do you think is better? I hope you’ll say 20 minutes. Because the faster your customer receives their order, the happier they’ll be. The lower the lead time, the more satisfied customers you’re going to get.
Lead Time Equation Using Little’s Law
From our Little’s law equation, we can isolate lead time and come up with this formula:

Lead time is equal to the number of Work-in-Progress items divided by the number of units completed per unit of time or throughput. It is important to note that lead time will be consistent with the unit of measure used for throughput.
From the equation above, we can say that lead time is affected by the increase or decrease of either WIP or throughput.
If we assume throughput remains constant, increasing WIP will increase lead time. Decreasing it will reduce lead time. Inversely, if we assume WIP remains constant, increasing throughput will reduce lead time. Decreasing throughput will increase lead time.
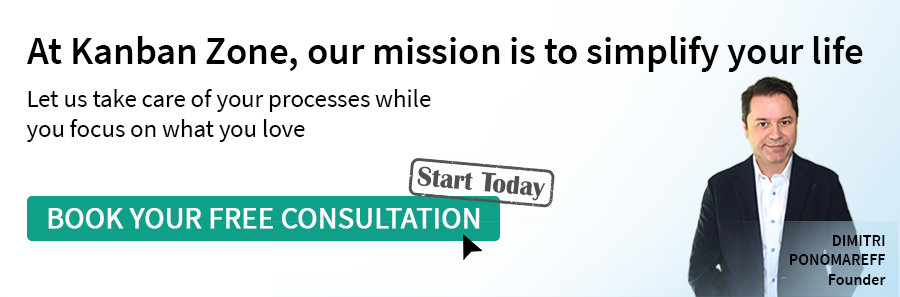
Little’s Law Example: Calculating Lead Time in Software Development
Little’s law can easily be modeled with physical processes. But knowledge-based work like software development isn’t a common Little’s law example. Perhaps it’s harder to visualize an intangible process. But this is where Kanban systems become extremely useful. Modeling a software development process into a Kanban system allows teams to represent their work by using Kanban cards. So WIP in terms of software development could refer to user stories, bugs, feature requests, and others that will flow through the Kanban system via cards. The team can then measure their WIP, throughput, and lead time for a given period.
Let’s say a software development team has an average throughput of 5 user stories per week. And for their next release, they need to tackle 20 user stories. Using our lead time formula, this means it will take the team 4 weeks to complete all their backlog.

But what if the team was given a hard deadline of only 2 weeks to finish? To achieve this, they would need to find a way to increase their throughput to 10 user stories per week.

But what if the team could only do 5 user stories per week for this project as they are also working on other projects? This means they would have to sacrifice some items on the backlog and probably negotiate to deliver the most important ones first. Lowering their WIP to 10 user stories will increase their chances of meeting the 2 week lead time.

Improve Lead Time with Little’s Law
Apart from using Little’s Law for estimating and measuring process performance, the real benefits are enjoyed when teams use the data gathered to improve process performance. It’s about knowing and understanding what hinders a team to shorten their lead time and increase their throughput. Using our Little’s law software development example, teams can further probe and ask these questions:
- Are there bottlenecks in the process that lowers your throughput?
- Are we working on too many items all at once (WIP) and things are taking longer to complete?
Little’s law can be used to diagnose process inefficiencies and shortcomings. Once these problems are surfaced, teams can devise strategies to improve their process performance.
To reduce lead time you can:
- Reduce the number of items you’re working on at any given time (WIP)
- Improve the average completion time (throughput) of items or increase the number of items you’re able to complete at any given time
The first one can be achieved by religiously observing WIP limits. Improving throughput can be done by taking out bottlenecks, unnecessary queues, and ensuring there are enough man and machine capacity for your work volume.
Reducing lead times is not only a metric that teams should aim to achieve. Teams must understand that lead times directly affect customer satisfaction and their overall success. Little’s law is only a tool for teams to know how they measure up against customer’s expectations. The real magic happens when teams decide to take action to streamline their process, deliver faster, and achieve high levels of customer satisfaction.
Learn to Work Smarter, Not Harder!
Get our top articles weekly.
Table Of Contents
Discover many more posts…