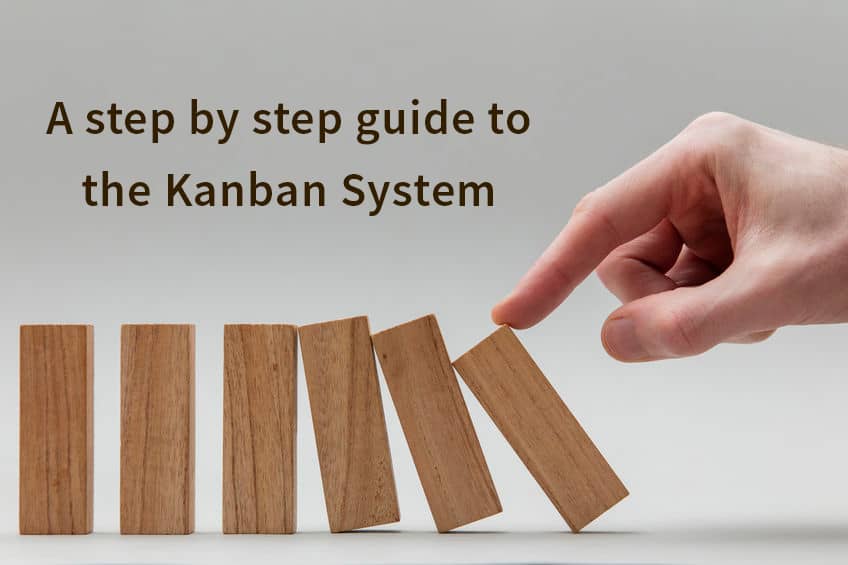
In order to explain the Kanban system, we must first explain the word Kanban and the concept of a pull system. Then we will rely on Toyota’s expertise in using Kanban to appreciate the philosophy of complete elimination of waste (Just-in-Time) and their six rules for an effective Kanban system. Lastly, we will illustrate the system with inventory management typically found in the manufacturing world, versus a Kanban system without inventory in areas like software development and business processes.
The meaning of the word Kanban
The word Kanban can be translated into English from its Japanese origin as the word “signboard” or “visual card”. Therefore a Kanban system relies on visual cards that hold key information for the system to create, track and deliver these cards.
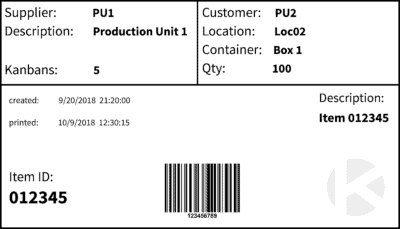
A physical Kanban card example
Push vs pull system
The more traditional push system requires the ability to forecast the behaviors of customers to predict how much to produce. With this approach, large batches of materials will get pushed into the system and a material requirement planning as well as a schedule will need to be developed to push these materials through the system. Just like the Waterfall method for project management, this push system is about big bang deployments, instead of Agile methods that seek to deploy small iterative releases. This is important to keep in mind as we explore Kanban systems without inventory.
The pull system used in Kanban, starts instead from a real customer demand (not a prediction), that causes the system to respond by signaling through Kanban cards the need for the preceding process to pull in exactly what is needed to respond to a customer’s demand. Each process works with the preceding process to continue to request only what is needed and nothing more. Please note that vendors interacting directly with the customer will often set up “order points” to request small batches of products, instead of a single product.
Now that we understand that Kanban uses a pull system and that visual cards are used to trigger actions from specific processes, we can explore how Toyota has been perfecting it.
Kanban system with inventory management
When materials are involved in a Kanban system, the Kanban can be a card or a bin. In this article, we will focus only on cards. As a quick note, using bins instead of cards simply means that an empty bin is used as a signal to be replaced by a full bin and the empty bin is sent for replenishment. When using a card, the card is attached to a batch of material and it simply moves between processes.
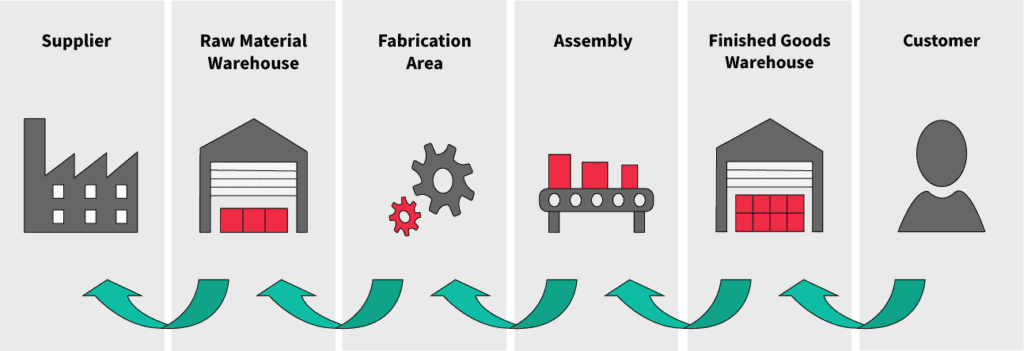
Kanban system example for a manufacturing process
In the example above, there are 6 steps (or processes) and 5 types of Kanban. Let’s imagine a store that sells hats and a customer just bought the very popular Multi-Colored Propeller Cap, known internally as the MCPC product code.
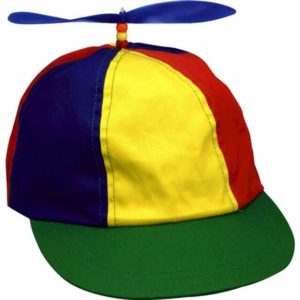
Multi-Colored Propeller Cap
Once the store completes the sell, the system recognizes that there are only 5 of these MCPC left, which is the order point for a new batch of 10 MCPC. The Customer Kanban signals to the Finished Goods Warehouse the need for 10 MCPC. That warehouse sends the new batch of 10 MCPC to the store, but also signals the need for a Finished Goods Kanban from the Assembly Area. This loop between 2 processes is known as the Kanban loop that ensures that materials are always available just-in-time.
Each process requests from the preceding process exactly what it takes to create 10 MCPC by using the Kanban type that contains all the information needed to fulfill 10 MCPC.
This is how you can replenish a Multi-Colored Propeller Cap using a Kanban system.
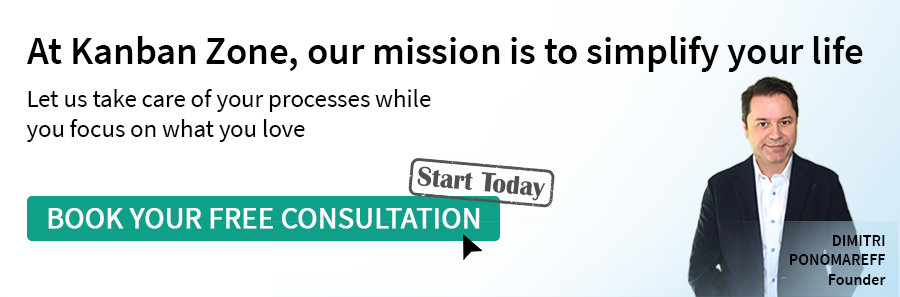
Toyota’s Just-in-Time philosophy and six rules for an effective Kanban system
Kanban is at the heart of the Toyota Production System (TPS), but the inspiration for creating the Kanban system at Toyota came from observing the way customers interact with products at supermarkets. The concept is simple, customers only take what they need from a supermarket, and the supermarket must always have products available for the customers. This fine balance between running out of products and not having too many products is called Just-in-Time.
The philosophy of complete elimination of waste (or Just-in-Time) means that we produce “only what is needed, when it is needed, and in the amount needed.” Applied in manufacturing, it will be critical to manage inventory levels to prevent waste. Below is the brief version of the six rules for an effective Kanban system as defined by Toyota:
- Never pass on defective products
- Take only what is needed
- Produce the exact quantity required
- Level the production
- Fine-tune production
- Stabilize and rationalize the process
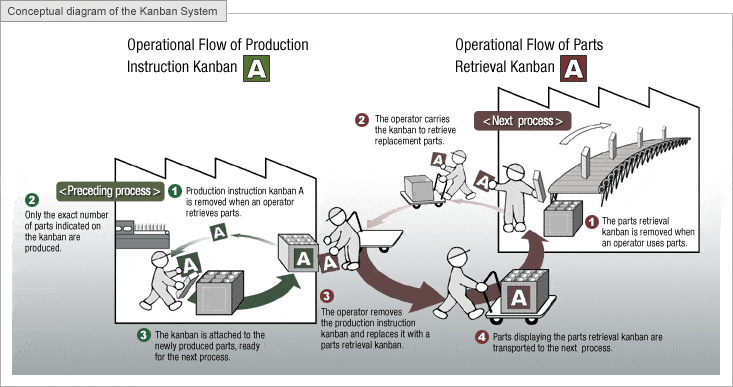
Toyota Production System (TPS) – source: toyota-global.com
Equipped with all the foundational concepts associated with Kanban, it’s time to put all the pieces into action and see a Kanban system actually works in practice.
Kanban system without inventory management
When it comes to applying Kanban to software, there are no materials being moved between processes, instead it’s only information and/or code that moves from ideation to completion. Since most organization use Agile to develop software, the focus is on delighting the customer and therefore a customer can also create a Kanban that signals the need to create/modify software.
The cards represent work that can have types like user stories and defects. Each type of card has the required information to complete the work. For example, a user story has acceptance criteria and defects steps to reproduce.
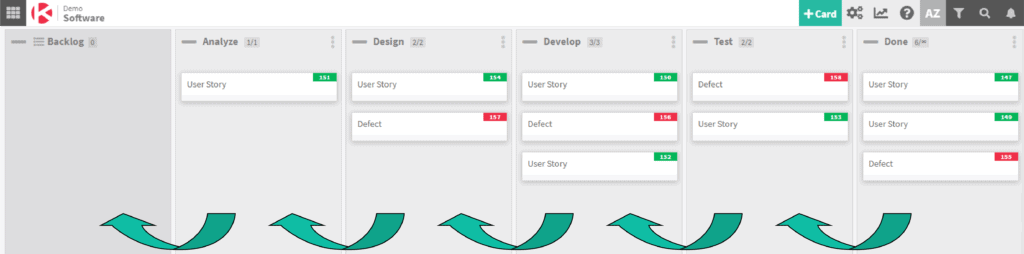
Kanban system example for a software process
The board example above illustrates how Kanban would be visualized on a board with cards that flow using a pull system. In this case, a card moving to the Done column represents a customer receiving new software. The same pull system takes place, by looking at the previous process (column on the board) and pulling a card from that process… All the way to the first column on the board, where the Backlog acts as the Supplier in the manufacturing example with the MCPC.
This Kanban system must also provide a way to level the production, so this is accomplished by setting Work In Progres (WIP) limits. Each WIP column has a quantity that the team fine tunes until they establish the ideal flow of work.
Although we used software as the example for this Kanban system, we could have mapped a sales, marketing, or any process you can imagine.
Are you ready to create your own Kanban system?
We believe that almost anything can benefit from using a Kanban system. If you seek to increase productivity, eliminate wasteful activities and continuously improve the way you work, then look no further than Kanban. It’s a proven method that truly creates positive results. If you are ready to start using this methodology, then build your online board for free and leverage our team of Kanban experts to help you design the ideal Kanban system.
Learn to Work Smarter, Not Harder!
Get our top articles weekly.
Table Of Contents
Discover many more posts…